防爆高速電機典型故障與解決方案
2025-05-24 10:25:58
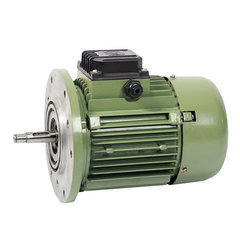
防爆高速電機(Explosion-Proof High-Speed Motor)廣泛應用于石油、化工、煤礦等易燃易爆環境,其核心要求是防止電機內部電火花或高溫引發外部爆炸性氣體燃燒。由于高速運行(轉速通常≥3000rpm)和防爆設計的特殊性,其故障模式和解決方案具有顯著特點。以下從典型故障、原因分析及解決方案展開論述。
一、典型故障分類與原因分析
故障類型典型表現根本原因影響
軸承過熱/失效 軸承溫度>120℃,噪聲異常,振動加劇 1. 潤滑脂變質或不足
2. 高速下軸承預緊力不當
3. 防爆密封摩擦阻力過大 軸承卡死、電機停機,嚴重時引發防爆殼體變形
絕緣擊穿 電機繞組對地短路,冒煙或燒毀 1. 防爆腔體內粉塵堆積導致局部放電
2. 高速運行下繞組振動疲勞
3. 防爆涂層老化 電機報廢,可能引發防爆失效
轉子不平衡 振動幅值>5mm/s(ISO 10816標準),軸溫升高 1. 高速旋轉下轉子動平衡精度不足
2. 防爆密封件脫落導致質量偏心
3. 軸彎曲 軸承壽命縮短,嚴重時引發防爆殼體開裂
防爆密封失效 防爆腔體內壓力異常,泄漏檢測報警 1. 密封圈老化或磨損
2. 高速旋轉下密封面離心力作用
3. 安裝時密封面損傷 爆炸性氣體進入腔體,失去防爆性能
冷卻系統故障 電機溫升>80K(F級絕緣標準),功率下降 1. 防爆結構限制散熱通道
2. 冷卻風扇失效
3. 冷卻介質(如空氣)流通受阻 電機過熱燒毀,絕緣材料加速老化
二、解決方案與實施要點
1. 軸承過熱/失效
優化潤滑管理:選用耐高溫、低摩擦的合成潤滑脂(如聚脲基潤滑脂,滴點>250℃)。
強制潤滑系統:高速電機(>10000rpm)建議采用油氣潤滑或噴油潤滑,減少摩擦熱。
預緊力控制:通過彈簧預緊或液壓預緊裝置,動態調整軸承預緊力,避免高速下預緊力衰減。
密封結構改進:采用磁性流體密封或迷宮密封替代傳統橡膠密封,降低摩擦阻力(摩擦功耗降低30%以上)。
2. 絕緣擊穿
防爆腔體清潔:定期清理防爆腔體內粉塵(建議每半年一次),采用防爆型吸塵設備。
涂覆防電暈涂層(如納米級SiO?涂層),提高局部放電起始電壓(>5kV)。
繞組加固:采用環氧樹脂真空浸漬工藝,減少高速振動下的絕緣層微裂紋。
繞組端部加裝彈性綁扎帶,吸收振動能量。
3. 轉子不平衡
高精度動平衡:動平衡精度等級提升*G1級(ISO 1940標準),殘余不平衡量<0.5g·mm/kg。
采用激光動平衡儀,實現轉子在線平衡調整。
防爆密封件固定:密封圈與轉軸采用過盈配合+卡簧固定,防止高速下脫落。
定期檢查密封件緊固狀態(建議每月一次)。
4. 防爆密封失效
密封材料升級:密封圈采用氫化丁腈橡膠(HNBR),耐溫范圍-40℃*150℃,抗老化性能提升50%。
密封面涂覆耐磨涂層(如DLC類金剛石涂層),硬度達HV2000以上。
安裝工藝優化:采用液壓壓裝工藝,確保密封面壓裝力均勻(誤差<5%)。
安裝后進行氣密性測試(壓力0.5MPa,保壓30min無泄漏)。
5. 冷卻系統故障
強制風冷優化:防爆電機外殼設計散熱翅片,增大散熱面積(比傳統結構增加30%)。
采用防爆型軸流風扇,風量提升20%,噪聲降低5dB(A)。
水冷系統應用:對于功率>200kW的高速電機,采用水冷夾套結構,冷卻效率提升50%。
冷卻介質選用乙二醇水溶液(防凍、防腐蝕),流速控制在1-2m/s。
三、預防性維護策略
振動監測:安裝在線振動傳感器,實時監測軸承、轉子振動狀態,閾值設定為ISO 10816標準的70%。
溫度監控:軸承部位埋設Pt100溫度傳感器,超溫報警閾值設定為110℃。
潤滑周期管理:根據工況調整潤滑脂補充周期(高速工況下每2000小時補充一次)。
防爆性能年檢:每年進行一次防爆性能檢測,包括外殼耐壓試驗、密封性測試等。